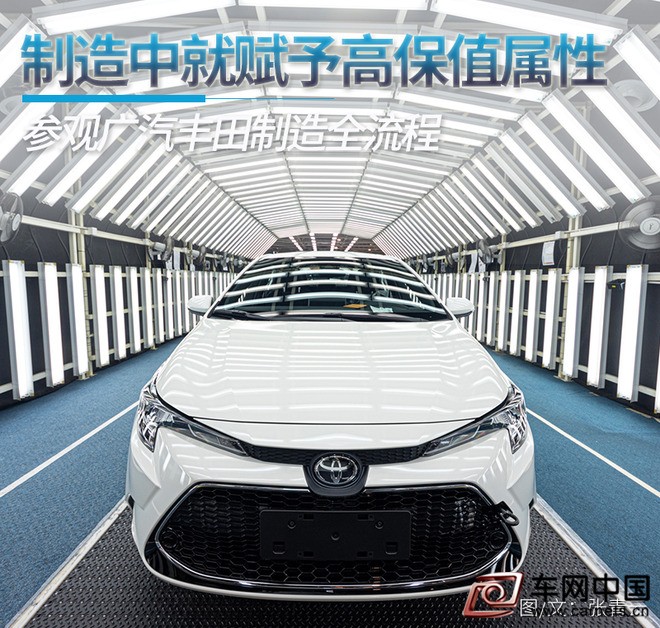
借着本次广汽丰田工厂开放日,有幸参观了广汽丰田研发中心、广汽丰田发动机有限公司以及广汽丰田第三生产线,这让我对广汽丰田的高品质制造有了更深一步的了解。(工厂内无法自行拍摄图片,图片均由官方提供,下文中可能会出现图文不符的情况)
首先在设计环节,广汽丰田的每一款车,如果需要做出改动,都要经过丰田总部,丰田董事长的批准,而这个设计在投产之前也要通过丰田的耐久度实验以及全球品质检查。
众所周知,汽车是由无数的零部件组成的,而零部件有些是供应商直接提供的,有些则是由工厂自己制造的。

铝制板材具有时效性,需要在规定的时间内完成冲压变形,否则就无法进行冲压,而且铝板不具备磁性,机器在“拾取”板材的时候就无法像吸钢板那样快速高效的吸取。甚至铝的一些特性也给制造带来了一定的难度,铝板的延展性低,冲压需要掌握“技巧”,否则就会开裂,铝材直接报废,而且铝材需要在更干净的环境下冲压,0.5mm直径的碎屑就会让铝板在冲压的时候产生麻点,影响使用。
为了避免这些问题,广汽丰田自主研发了吹气分离装置、模具吸尘装置、特殊的切刀,让铝材可以变成设计师喜欢的模样。
其实广汽丰田在零部件上除了对自己有高要求以外,作为广汽丰田的供应商“也不容易”,他们的生产流程和标准都必须要和丰田保持一致,广汽丰田发动机制造有限公司就是很好的例子。
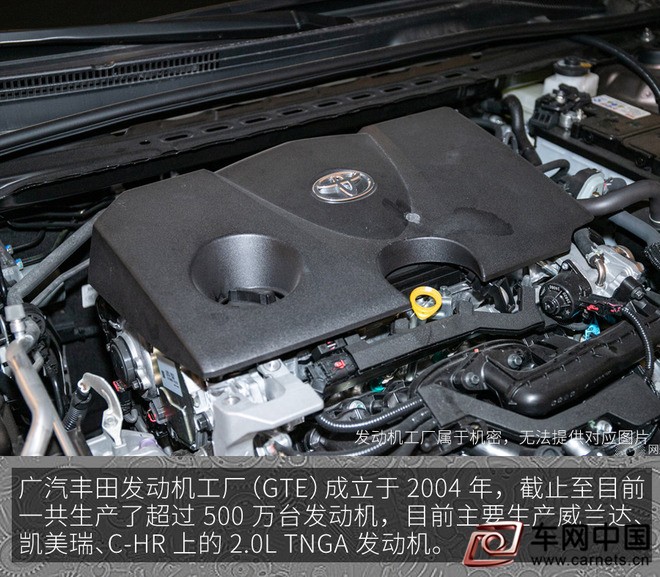
此外,在铸造工序,针对会影响产品品质的铝液、模具温度、脱模剂量、冷却水量等各种制造条件,会对每一台设备进行管理,以确保品质。
广汽丰田以及其供应商在所有生产流程中都采用了丰田特有的自工序完结体系,简单的来说,在每一个生产或者是组装的流程中,都会有人或者机器作为该步骤的质检,及时的将不良的产品剔除,避免不良品流进下一个环节。


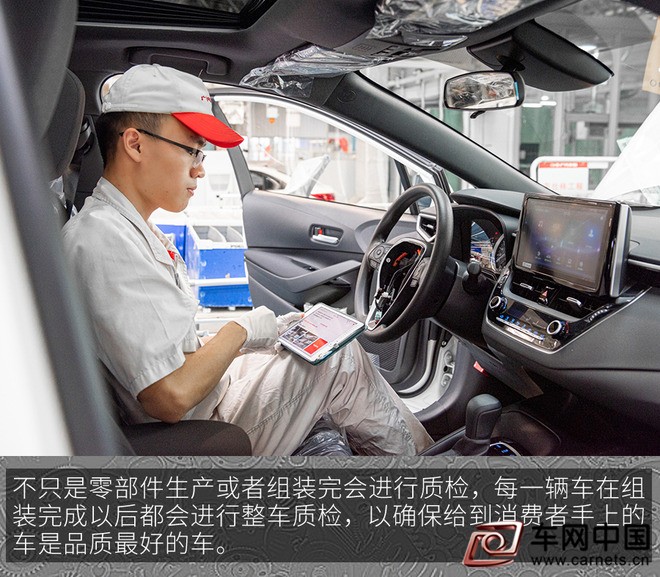

第一就是不留库存,无论是车还是零部件都不留库存,生产的零件及时使用,每一辆生产线上的车都是有订单才排产(相当于这款车就是为了这个顾客打造)。用生产人员的话术是这么说的,我们不能保证100%的合格,即便是99.999%的合格率一样还是有可能会有0.001%的不合格产品,我们及时把产品交付出去,这个问题就能更早的发现,以便我们做出改善,而不是这个产品因为积压在库存里,我们没法发现。实验室毕竟不是万能的,它只能模拟出99.99%的场景,但是真正的用车,还是要交给消费者,一旦发现问题,我们会及时修正。
第二就是品质监查。
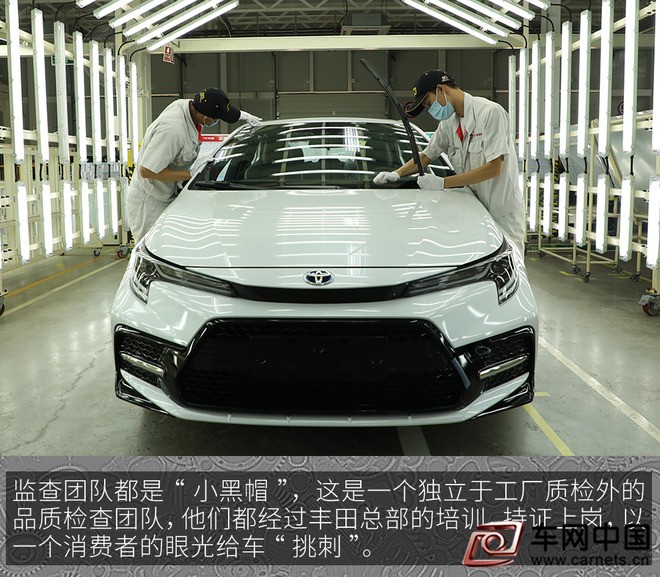
广汽丰田对自己近乎“变态”的质检要求,其实也换来了好成绩。
一、生产线一次合格率98.9%
生产线一次合格率,即车辆下总装线就打合格证直接出厂的比率达到98.9%,高于行业平均水平近10个百分点。

整车全数检查每一百台只有一件不良(指外观瑕疵,包括脏污等)。
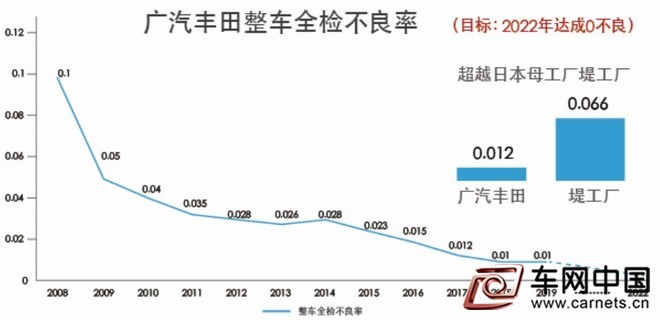
广汽丰田对品质管理的精髓也灌注到供应商身上。2019年,广汽丰田供应商零部件不良率为0.36PPM,即100万个部品中只有0.36件不良。
